Industrial 3D printing in xxxl format
Printing aerospace prototypes in XXXL format
Do you need XXXL components without long waiting times, cost-efficiently and entirely according to your requirements?
We have the solution. This is QUEEN 1.
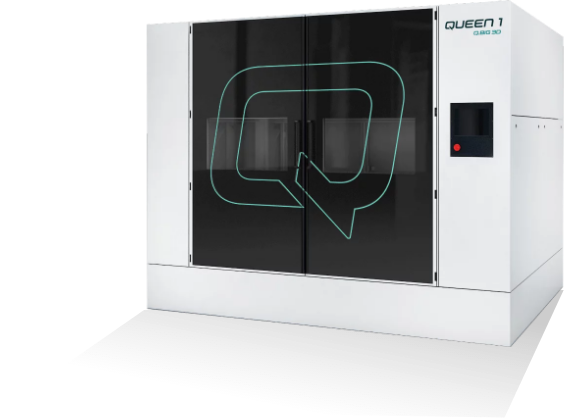
Project of a modular 3D full-flight simulator in detail
Creating oversized plastic components additively offers significant advantages for the tool-less production of small and medium-sized series. The key to achieving this lies in the VFGF process (Variable Fused Granulate Fabrication) developed by Q.BIG 3D
3D printing with plastic granulate makes it possible to process technical plastics with the desired properties such as rigidity. Melting in a specially developed screw extruder enables higher throughputs, which significantly reduces the printing time.
With the VFGF process, high-resolution printing is only used where it is necessary – for example on the surface. Inner volumes are quickly filled with thicker lines. This flexibility means that surfaces that are easy to paint and features such as integrated cable ducts or local reinforcement on door channels can be combined in one construction job.
Inexpensive plastic granulate in its raw form and the high output rate of the machine mean that components can be produced cost-effectively without having to invest in expensive tools or storage.
Thanks to a completely digital process chain from the 3D design to the finished product, without tool production and manual lamination, the lead time from order to execution can be greatly reduced.
The results in detail: Before and after finishing
Discover the impressive transformation of our 3D-printed full-flight simulator for the helicopter cockpit – from the first print to the high-quality finished end product. Experience how precisely 3D printing on the Queen 1 creates parts that impress in terms of quality and appearance after the careful finishing process.
Anything is possible. Let’s go!
Any paint shop can paint the 3D-printed parts. Thanks to the detail mode, the surface of the components is printed so well that a subsequent painting process of filling, sanding and painting can be carried out by any specialist.
Make the future of your industry – now!
With the QUEEN 1, you can redefine industry standards. Be the pioneer that breaks new ground with large-format, self-printed components. Shorter, faster, more innovative – transform your production and become a pioneer of change.
2980 x 2370 x 2580 mm (118 x 93 x 102 in) (width x depth x height)
1700 x 1050 x 1050 mm (67 x 41 x 41 in) (XYZ)